For any business manufacturing goods, loss is one of the major sources of preventable expenses. Faulty products can be caused by all manner of things, and some products are going to be more at risk of cross-contamination, where contact between materials used in the manufacturing process can cause them to lose their integrity. What can you do to prevent this?
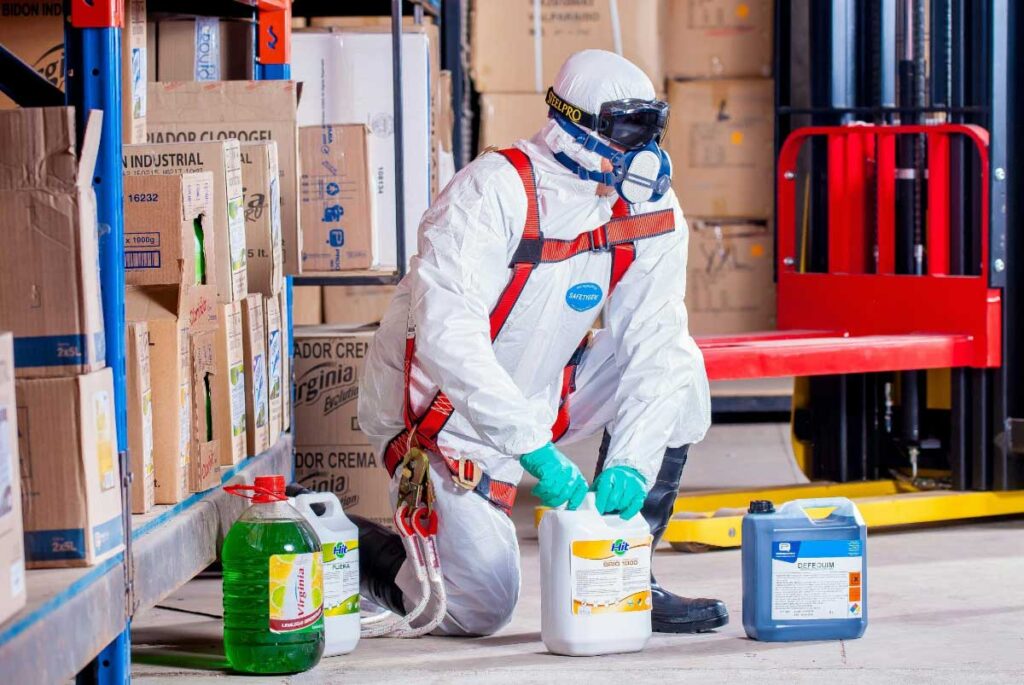
Using Separate, Labelled Storage
Preventing cross-contamination in manufacturing starts with the organization and clear demarcation of storage areas. Each type of material, whether raw ingredients, finished products, or hazardous substances, should be stored in separate, clearly labelled areas. This segregation minimizes the risk of mixing incompatible substances, which can cause contamination, spoilage, or hazardous reactions. Clear labelling, with detailed information about the contents and handling requirements, ensures that workers can easily identify and correctly manage materials. Implementing this practice as part of a broader inventory management system helps maintain high safety and quality standards throughout the manufacturing process.
Find Secure Containers
Secure containers are vital for safely storing and handling materials, particularly hazardous chemicals. For example, chemical cabinets are designed to securely store chemicals, reducing the risk of spills, leaks, or unauthorized access. These containers should be robust, resistant to the materials they hold, and equipped with secure locking mechanisms. Using appropriate containers also involves regular maintenance checks to ensure they remain in good condition and provide the necessary protection. By investing in high-quality, secure storage solutions, manufacturers can significantly reduce the risk of cross-contamination and enhance overall workplace safety.
Preventing Leaks
Leak prevention is another critical aspect of preventing cross-contamination. Leaks can occur in various parts of the manufacturing process, from storage containers to piping systems. Utilizing high-quality gaskets and seals is essential to prevent leaks that could lead to contamination. Gaskets, which are used to create tight seals between two surfaces, should be chosen based on their compatibility with the materials they will contact. Choosing the right gasket material types is vital depending on the nature of the seal and component materials. Regular inspection and maintenance of these seals are necessary to identify wear and tear early and to replace any faulty components promptly. Implementing stringent leak prevention measures ensures that materials remain contained, safeguarding against contamination and maintaining product integrity.
Train Your Workers
Proper training for workers is fundamental in preventing cross-contamination. Employees should be well-versed in using personal protective equipment (PPE) and trained in the correct handling and storage of materials. Training programs should cover the appropriate use of tools and equipment, procedures for dealing with hazardous substances, and the importance of hygiene and cleanliness. Regular refresher courses and drills can help reinforce these practices, ensuring that all workers remain vigilant and competent in maintaining safety standards. Educating the workforce on the risks of cross-contamination and the measures to prevent it creates a proactive safety culture that underpins the entire manufacturing operation.
Investing the time and money necessary to prevent cross-contamination may seem like an expense at first but compared to the money you could save in loss prevented can more than make up for it.