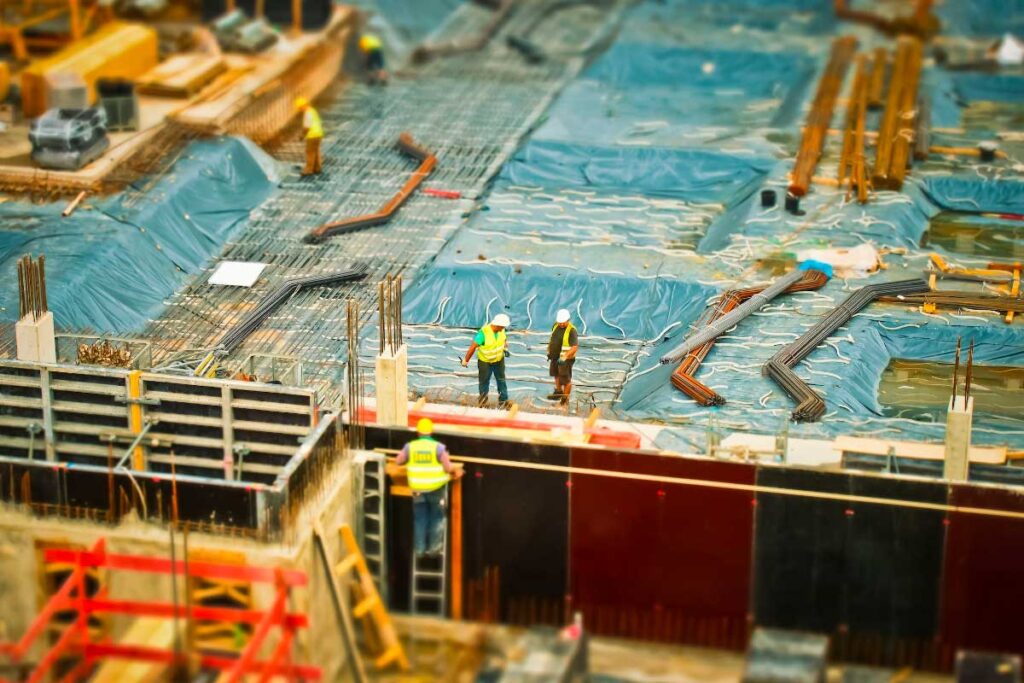
With the US and Canadian construction sector poised for growth in 2024, meeting demand and expectations without avoiding falling victim to the ongoing labor shortage will serve you well and help you take advantage of the expected upward trend in the intraday this coming year.
So, how can you put yourself in the right position to not only survive but thrive as a construction company?
Know The Industry
Keeping on top of industry changes and news, as well as cost fluctuations, materials are predicted to rise around 3-6%, and labor costs are looking to grow up to 5%. You can make more informed choices and accurate estimates to remain competitive without pricking yourself out of the market.
Knowing what to expect, how others are performing, and what new regulations your state is implementing will allow you to stay ahead of the game and make any required changes to remain compliant.
Invest In Your Team
The US construction industry is facing a severe labor shortage of around 650,000 workers, slowing projects across the country. There are multiple reasons for this, including boomers reaching retirement age and the slower uptake of younger generations taking up the trade. But investing in the team you have, improving their skills, giving them the proper training and tools, and being appreciative of their efforts on your behalf can help you avoid being the next construction company to face staff shortages.
Have incentives for newbies to get started and learn the ropes for your more experienced workers, offer foreman training for those who meet the criteria for a good foreman, and ensure everyone can work alone and as a team to get the job done as required without too much hand holding.
Improve Procurement Times
There is often a long lead time between sourcing the materials and having them ready to use, and the longer it takes for you to get started, the more money it will cost you in the end.
The best way for you to reduce procurement times is simply to maintain better relationships with the suppliers you use so you can expedite delivery and ensure that when you do need materials or tools, you get them as fast as possible. And if there is a shortage with your preferred supplier? It pays to have a backup you can use; don’t limit yourself to your options; instead, develop and maintain multiple relationships with vendors to enable you to get when you need without the long wait times.
Maintenance
It should be common sense that having and maintaining the right equipment is going out to make yourself much easier. Having an effective maintenance plan means you can be confident everything is in good working order, and you won’t be at risk of breakdowns or setbacks due to incorrectly maintained equipment, tools, or machinery.
What regular maintenance does is reduce downtime from unexpected failures or damage, lower the cost of repairs as you find issues faster and can repair them before they deteriorate, and allow you to plan your schedule better. For example, if something does need to be out of action for repairs, you will have an advanced warning and can either move around planned work or look at hiring the same equipment to avoid losing time and money during the repair.
As demand for construction grows, being prepared with efficient operations and a skilled team will set you apart from competitors. For optimizing internal communication and documentation, tools like ProWritingAid can help ensure your writing is clear and professional, keeping your business running smoothly.